Assembly Line: Definition, Pros, Cons & Examples
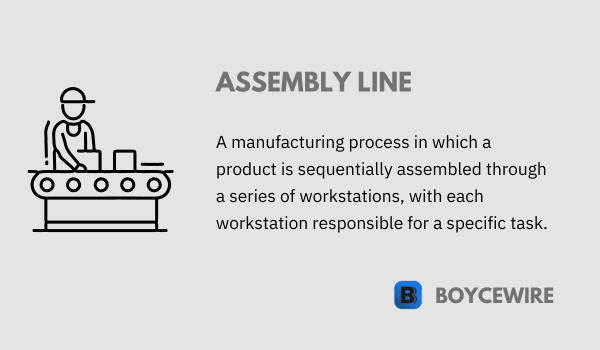
What is an Assembly Line?
In the world of manufacturing, few innovations have been as transformative as the assembly line. By dividing labor into discrete, repeatable tasks performed in a linear sequence, the assembly line has dramatically increased productivity and efficiency in countless industries. It has reshaped the way goods are produced and has played a pivotal role in the rise of mass production.
The concept of the assembly line is often associated with Henry Ford and the automotive industry. However, its impact extends far beyond that, with applications in fields as diverse as food processing, electronics manufacturing, and even software development. Despite criticisms and challenges, the assembly line remains a cornerstone of modern industry, continually evolving as new technologies are integrated into the production process.
Key Points
- An assembly line is a production system that allows for efficient and standardized manufacturing processes.
- It involves dividing the production of a product into a series of tasks, which are performed by specialized workers or machines stationed along the line.
- Each worker or machine is responsible for a specific task, and the product moves from one station to another until it is fully assembled.
Understanding the Assembly Line
At its core, an assembly line is a manufacturing process in which interchangeable parts are added to a product in a sequential manner to create a finished product. The concept is based on the principle of division of labor, a key component of industrial production. Rather than having a single craftsman or team of artisans create each part of a product from start to finish, each worker on an assembly line is assigned a specific task that they repeat on each unit that passes through their station.
In an assembly line, the product moves along a conveyor belt or similar mechanism, stopping at each workstation along the line. At each station, workers or automated machines perform specific tasks, such as attaching a part, assembling a subcomponent, or carrying out a quality control check.
The assembly line design allows for specialization, as each worker becomes highly skilled at their particular task. This can lead to increased efficiency, as workers do not need to switch between different tasks and tools. It also allows for the use of specialized machinery, further increasing productivity and consistency.
There are several key concepts related to the assembly line:
- Standardized Parts Assembly lines rely on parts being standardized, meaning each part is identical and interchangeable. This reduces errors and speeds up assembly.
- Sequential Assembly The assembly process is broken down into a sequence of steps, each carried out in a specific order. This order is typically designed to optimize efficiency and minimize wasted movement.
- Automation Many modern assembly lines use automated machines or robots to perform certain tasks, especially those that are dangerous or require high precision.
- Quality Control Assembly lines often include steps for inspecting and testing products or components to ensure they meet quality standards.
The assembly line is an integral part of many manufacturing processes, from automobile production to electronics manufacturing and more. It has revolutionized the way products are made, enabling mass production and dramatically lowering the cost of goods.
History of the Assembly Line
The concept of the assembly line has a rich history, rooted in the earliest days of industrialization and evolving alongside advancements in technology and business practices.
- Early Implementations The basic principles of the assembly line can be traced back to ancient times. For instance, in ancient Rome, production processes were often divided into separate tasks carried out by different workers. However, these early forms of assembly line production were limited in scale and efficiency.
- Industrial Revolution
The assembly line concept took a significant step forward during the Industrial Revolution in the late 18th and 19th centuries. Innovations such as the interchangeable parts system used in the manufacture of muskets for the U.S. military in the early 19th century brought the idea of standardized parts to the forefront of manufacturing.
- Automotive Industry and Henry Ford The assembly line as we know it today truly came into its own with Henry Ford and the Model T in the early 20th century. Ford did not invent the assembly line, but he refined and popularized it, implementing it on a grand scale at his Detroit factory. In 1913, Ford introduced the first moving assembly line for large-scale manufacturing. This innovation drastically reduced the time it took to build a car, from more than 12 hours to about 2.5 hours. This dramatic increase in productivity allowed Ford to reduce the price of the Model T, making it affordable to the average consumer and revolutionizing the automobile industry.
- Modern Developments In the years following Ford’s innovation, the assembly line continued to evolve. During the mid-20th century, Toyota developed the concept of “lean manufacturing,” an approach designed to minimize waste and inefficiency in the production process. This concept has had a significant impact on assembly line production and is widely used in industries around the world today.
More recently, the advent of advanced robotics and artificial intelligence has ushered in a new era for assembly line production. Robots are now commonly used in assembly lines to perform tasks that are dangerous or highly repetitive. At the same time, the principles of the assembly line are being applied beyond traditional manufacturing, for instance, in areas like software development and service industries.
From its early beginnings to its modern incarnations, the assembly line has transformed the manufacturing landscape. It remains a cornerstone of industry and continues to evolve to meet the needs of modern production processes.
Types of Assembly Lines
There are several different types of assembly lines, each designed to suit different kinds of products and manufacturing goals. The primary types of assembly lines include:
- Single-Station Assembly Lines This is the simplest form of an assembly line, in which a single worker or a group of workers assemble a product from start to finish. This type is usually used for complex, less standardized products or for small scale production.
- Sequential Assembly Line The most common type, it follows a linear sequence where the product moves from station to station, and each worker or machine performs a specific task. This is the type often associated with automobile manufacturing or electronics production.
- Progressive Assembly Line Also known as a straight line or continuous assembly line, this is similar to the sequential assembly line. However, in a progressive assembly line, the product moves continuously rather than stopping at each station. This can lead to higher production speeds.
- Modular Assembly Line This involves several parallel assembly lines, each of which assembles a module or component that will be added to the final product. This type of assembly line is often used in the automotive industry, where different subsystems like the chassis, engine, and interior are assembled separately before being combined.
- U-Shaped Assembly Line In a U-shaped assembly line, workers and machines are arranged in a U shape. This design often allows workers to handle more than one task on the line, improving flexibility and efficiency. It also facilitates better communication and cooperation among workers.
- Automated Assembly Line This is an assembly line where most or all of the assembly tasks are performed by automated machines or robots. This type is common in industries where high precision or speed is required, or where the tasks are dangerous or repetitive.
The choice of assembly line type depends on various factors, including the nature of the product, production volume, the level of customization required, and the available technology. Different types of assembly lines can also be combined or modified to create a production process that meets specific manufacturing needs.
Advantages of the Assembly Line
The assembly line revolutionized manufacturing and has several distinct advantages:
1. Efficiency
One of the most significant benefits of the assembly line is increased efficiency. Assembly lines enable mass production, allowing businesses to manufacture large quantities of products quickly.
2. Cost Savings
By standardizing the production process and leveraging economies of scale, assembly lines can significantly reduce the cost per unit of a product. Lower production costs can translate into lower prices for consumers, thereby increasing demand for the product.
3. Labor Specialization
Each worker in an assembly line focuses on a specific task, allowing them to specialize and improve their efficiency and accuracy over time. This task specialization can lead to higher product quality and less waste.
4. Predictability and Planning
Assembly lines make the production process highly predictable, making it easier to plan and manage inventories, shipments, and other logistical aspects.
5. Technological Innovation
Assembly lines encourage technological innovation and the development of new production methods. Over time, this has led to advancements like automation and robotics, which further increase efficiency.
6. Job Creation
Although automation has replaced some jobs, the overall increase in production capacity often creates new jobs in areas like machine operation, maintenance, quality control, logistics, and management.
The assembly line is a proven method for efficient, large-scale manufacturing. However, it’s not suitable for all types of products or industries. Some products require customization or craftsmanship that may not be compatible with the standardized nature of assembly line production. Additionally, the assembly line can lead to repetitive work for employees, which may affect job satisfaction and well-being. It’s important to consider the specific needs and characteristics of a product or industry when determining the most appropriate manufacturing approach.
Disadvantages of the Assembly Line
While the assembly line has proven to be a revolutionary manufacturing process, it does come with some drawbacks:
1. Lack of Flexibility
Assembly lines are designed for mass production of a standardized product. This makes it difficult to accommodate custom orders or changes in the product design without disrupting the production process.
2. Repetitive Work
The tasks performed by assembly line workers are often repetitive, which can lead to worker dissatisfaction, low morale, and high turnover rates. Over time, this can also lead to physical ailments like carpal tunnel syndrome or other repetitive strain injuries.
3. Dependency on Each Step
In an assembly line, the entire production process can be delayed if one step or station breaks down or gets backlogged. This interdependence can cause problems if there is not sufficient redundancy or flexibility in the system.
4. High Initial Investment
Setting up an assembly line can require a significant upfront investment in equipment and facilities. This investment may not be feasible for small businesses or for products with uncertain demand.
5. Risk of Oversupply
Assembly lines are most efficient when producing large quantities of goods. However, if demand for the product drops or is overestimated, companies can be left with excess inventory that they need to store or sell at a loss.
6. Potential for Job Displacement
The increasing automation of assembly lines, while improving efficiency, can displace workers, especially those with low skill levels. This has led to concerns about job loss and income inequality.
While assembly lines have their challenges, many of these can be mitigated through effective management practices, careful planning, and by balancing the needs of efficiency with the needs of workers.
Examples of Assembly Lines
- Automobile Manufacturing The most famous example of an assembly line is the one created by Henry Ford for the Model T car in the early 20th century. Today, almost every car manufacturer uses some form of an assembly line to produce vehicles.
- Electronics Production Assembly lines are used in the production of electronic goods such as smartphones, computers, and televisions. These often involve a mixture of human labor and automated machinery to assemble delicate and complex components.
- Food Processing Many food products are produced on assembly lines, including packaged foods, canned goods, and prepared meals. Even bakeries and candy factories often use assembly lines to produce goods at scale.
- Clothing and Textiles Large-scale textile manufacturers often use assembly lines to produce clothing items. Each worker or machine along the line may be responsible for a specific part of the garment, such as sewing a seam, attaching buttons, or adding finishing touches.
- Appliance Manufacturing Home appliances like refrigerators, washing machines, and microwaves are often produced on assembly lines. These production lines involve both assembly and testing processes to ensure the quality and functionality of the appliances.
- Toy Manufacturing Large toy companies often use assembly lines to mass-produce toys. This process allows for the efficient manufacture of many identical items, ensuring consistency and quality control.
- Pharmaceuticals The pharmaceutical industry uses assembly lines to manufacture, package, and distribute medications at a large scale.
These examples demonstrate the broad application of assembly lines across many industries. While the specifics of the assembly line may vary from industry to industry, the basic principles of sequential task allocation, efficiency, and mass production remain the same.
FAQs
An assembly line is a production system where a product is manufactured by moving it through a series of workstations, with each workstation performing a specific task.
Assembly lines offer benefits such as increased productivity, faster production, lower costs, consistent product quality, and improved efficiency.
An assembly line involves dividing the production process into sequential tasks, with each task being performed at a specific workstation along the line. The product moves from one workstation to another until it is fully assembled.
Assembly lines are commonly used in industries such as automotive, electronics, manufacturing, and consumer goods.
About Paul
Paul Boyce is an economics editor with over 10 years experience in the industry. Currently working as a consultant within the financial services sector, Paul is the CEO and chief editor of BoyceWire. He has written publications for FEE, the Mises Institute, and many others.
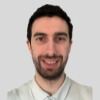
Further Reading
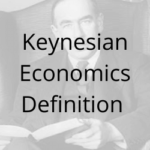
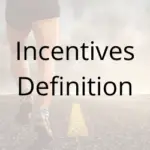
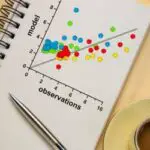